高性能双螺杆挤出机核心技术——传动部分
浏览次数:3221 发布时间:3/2/2023 4:34:02 PM |
  |
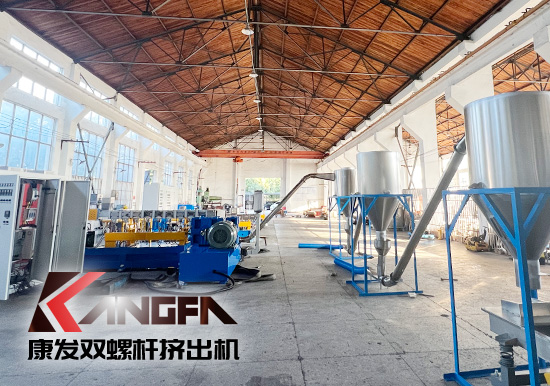
双螺杆挤出机与其他机型相比,一个显著的特点就是传动系统的不同。双螺杆挤出机要求在一个受限的空间内把动力平均地分配到两根螺杆上,这就是扭矩分配技术。不同的扭矩分配技术,决定了齿轮箱的承载能力、甚至于直接影响整机的寿命和性能。
传统的平行三轴式扭矩分配技术传统的平行三轴式扭矩分配技术是一种成熟的双螺杆挤出机传动技术,国外双螺杆挤出机的齿轮箱早期大多采用这种结构。如传统的平行三轴式传动原理图所示,来自电机的动力平行均匀地分配到A、B两输出轴上,即A、B轴各承担50%的扭矩。由于A、B轴中心距的限制,B轴上齿轮相对较小,传递的扭矩值受限。所以B轴齿轮是
双螺杆挤出机齿轮箱承载力的瓶颈,直接决定了齿轮箱所能传递的功率。
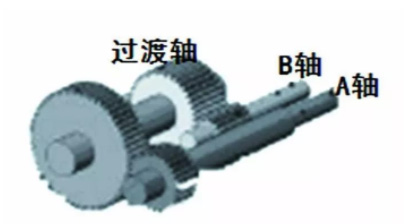
传统平行三轴式传动原理图
高扭矩平行三轴式扭矩分配技术为了提高B轴的输出扭矩,改进的结构在B轴上设计了两组齿轮传动,这样B轴输出的扭矩理论上是改进前的2倍,实现了高扭矩输出,亨舍尔公司的高扭矩齿轮箱就是采用这种结构。
高扭矩平行三轴式齿轮箱的优点1 这种结构中,A/B两输出轴及过渡轴中心都位于同一平面内,齿轮箱只有一个分型面,所以结构简单,装配方便;
2 过渡轴采用浮动布置,其上的两斜齿轮与B轴上的两啮合齿轮处于动态平衡状态,无需人为调整即可均载,传动可靠。
高扭矩平行三轴式齿轮箱的缺点1 安装B轴的轴孔细长,加工精度难以保证,尤其对于小功率齿轮箱,这个问题显得更为突出。
2 B轴上的轴承始终承受较大负荷,且为弯扭联合作用,B轴上轴承所承受的力随着输出扭矩的增加而增大,使轴承在受力磨损20000h后,达到齿轮轴和轴承的寿命极限,所以这种结构的齿轮箱寿命受B轴轴承的制约。
3 由于B轴始终承受较大载荷,加速了轴承的磨损,造成B轴的径向跳动不断增加直至失效,使该系统成为一个不稳定的动力系统。由于B轴的跳动,导致由其驱动的螺杆也不稳定,导致螺杆和机筒之间的间隙不均匀,造成物料在机筒内的停留时间不均匀,从而影响产品品质的一致性。
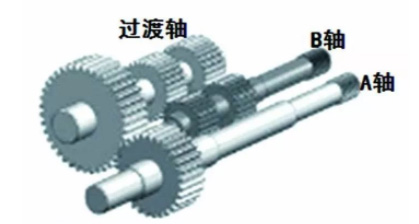
高扭矩平行三轴式传动原理图
双侧对称齿轮驱动式扭矩分配技术如双侧对称齿轮驱动原理图所示,输出轴A和平行三轴式一样,其上的轴承、齿轮等都有足够的强度,安全系数高。
而B轴上的齿轮依然受制于两螺杆的中心距,承载能力有限,这种结构提供的解决办法是将传递给B轴的扭矩等量分解到两个过渡轴C/D上,在输入端,过渡轴C/D上的齿轮同时与A轴上齿轮啮合,在输出端同时从上下两个方向对称地与B轴齿轮啮合,这样B轴齿轮在不增加齿宽的情况下,同时受到两个齿轮驱动,从而达到高扭矩驱动的目的。
双侧对称齿轮驱动式齿轮箱的优点1 由于两过渡轴C/D对称布置于B轴的两侧,B轴的齿轮仅受到切向力,径向力完全抵消,形成理想的力偶驱动。同时,B轴也仅承受纯扭矩,没有弯曲应力,彻底消除了B轴上径向轴承的负荷,B轴理论上永不磨损,使用寿命可达72000h。
2 该结构不仅实现了高扭矩输出,提高了生产效率,还增加了齿轮箱的使用寿命,更重要的是保证了扭矩分配系统的稳定性。由于B轴上的轴承不受径向力,从而不会发生因轴承磨损所带来的径向跳动,相应的也就不会引起螺杆的径向跳动,物料在机筒内停留时间的一致性好。
双侧对称齿轮驱动式齿轮箱的缺点1 该结构相对复杂,装配难度大,制造成本较高。由于上下两个过渡轴C/D与输出轴A/B不在一个平面上,这样给制造和装配都带来困难。
2 过渡轴C/D上齿轮与B轴齿轮啮合,必须人为调整,以确保两个过渡轴上的齿轮各自都真实准确地把总扭矩的25%传递给B轴齿轮,也就是保证两过渡轴齿轮均载,而且要确保在整个齿轮箱寿命期间,这个均载一直有效,这是这种结构齿轮箱成功运转的关键所在。如果均载不理想,或者不能长时间的维持这种均载状态,则直接影响齿轮箱使用寿命。
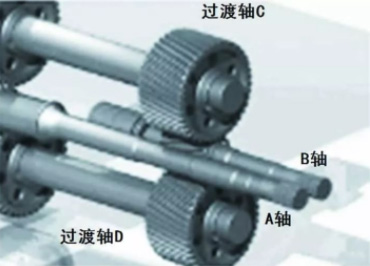
双侧对称齿轮驱动式传动原理图